    
Valve
Leak Detection using Acoustic
Emission
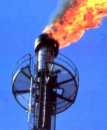 Site
experience has shown that 5-10% of valves leak, and 1-2% of valves cause
70% of total loss. Savings in excess of $100,000 per site are easily
achieved. Where gas recovery systems are in use, monitoring product
valve leakage helps to identify and estimate the extent of the
downgrading of valuable products to fuel gas due to valve leakage. This
is something previously identified by the flare, but goes unseen with
gas recovery in use. Cost savings are achieved in maintenance planning,
troubleshooting plant operations and monitoring of losses for
environmental purposes.
มล
procedures for the detection of leaks through valves have
been developed for use in refineries, chemical plants
and offshore platforms. It enables estimation of through-valve
gas losses and leak rate. Tests are carried out using
the PAC's 5131 portable leak detector and D9203IS sensors.
A more than 10-year database built up in cooperation with
BP (British Petroleum) relates acoustic signal level to
gas losses for various valve types (ball, relief, plug,
gate, globe, butterfly), of different valve sizes (1"
- 18") and working within 0.5 to 140 bar pressure
range.
Losses
Calculation
Using their
database, BP developed a calculation that estimates losses from the
input data. This is provided as part of the package in a spreadsheet
form, which makes use very easy on a PC. It is particularly useful on
large sites that have many hundreds of valves. It is also provided in
a graphical form for quick use out in the plant.
Advantages
-
Totally non-invasive.
-
Simple & Intrinsically
safe operation.
-
Portable instrumentation.
-
On-line measurement,
valve tested within seconds.
-
Savings up to $100.000
per site from loss control.
-
Cost reduction of
maintenance and plant operations.
-
Monitoring losses
for environmental purposes.
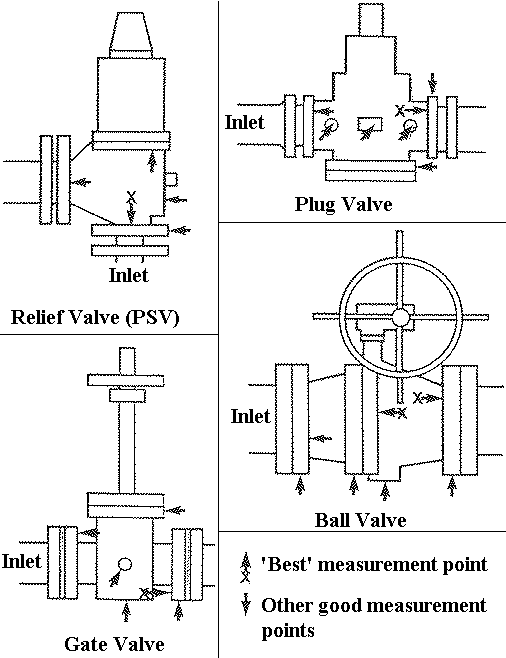
|